I spent the day with the Head of IT Operations Luca Chichiarelli and the Plant Maintenance Manager Angelo Mucci, and saw first-hand the complete production process from the raw material coming into the factory to the final product loaded onto forklifts and delivered to trucks for shipment. I was blown away and wanted to share some insights.
Wi-Fi challenges in manufacturing automation
The challenge that Del Conca faced with Wi-Fi was very real. They found that their regular Wi-Fi APs were not providing the reliable connectivity they needed – especially outdoors. They could not get the Wi-Fi signal through the pallets of ceramic stored throughout the facility. As their forklifts moved in and out of the facility, Wi-Fi connectivity constantly broke down due to lack of mobility as they roamed between indoor and outdoor Wi-Fi APs. They tried to improve coverage by deploying Wi-Fi with leaky linear RF cable hung on large existing posts to act as antenna to distribute the Wi-Fi signal, as pictured below.
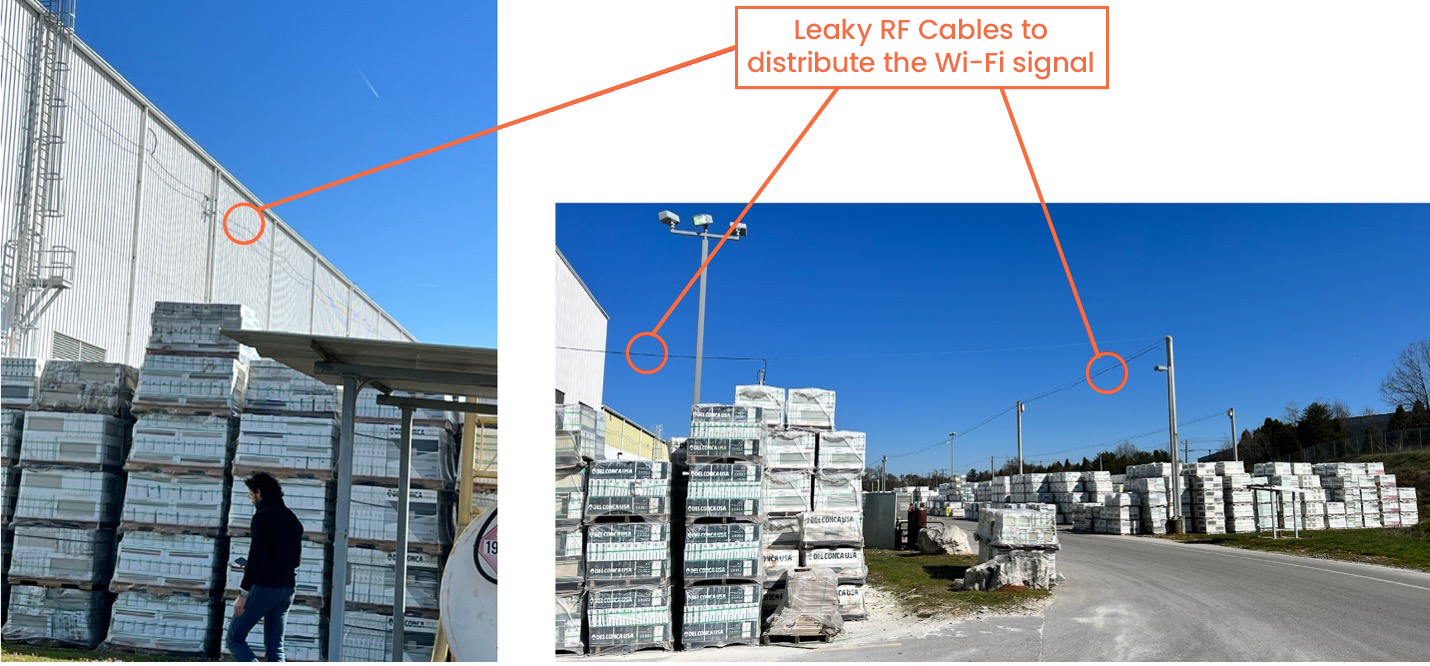
Inside the facility, Wi-Fi coverage was also patchy due to all the metal structures typical in any factory floor. Here’s a glimpse of what it looks like inside Del Conca:
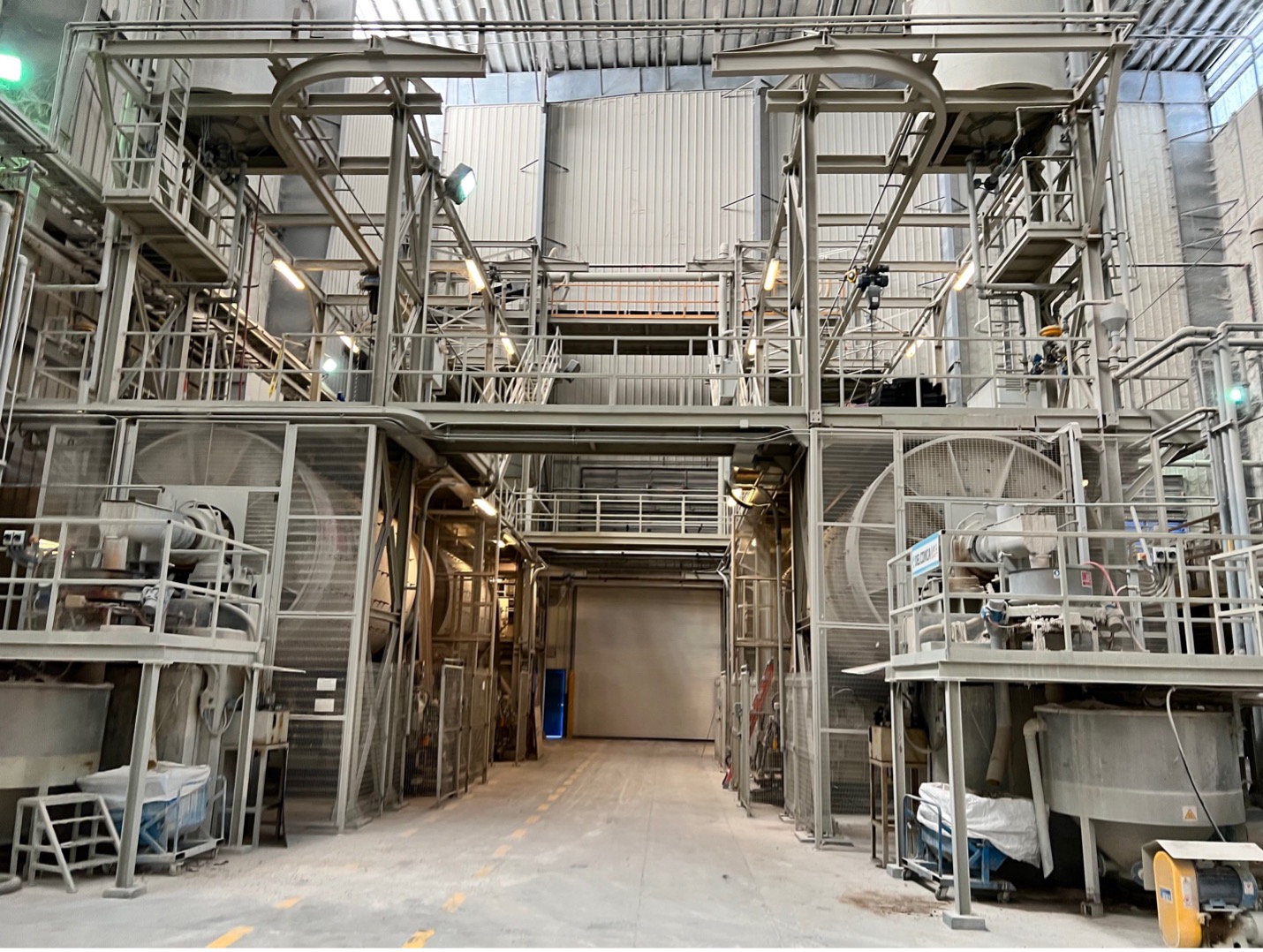
Unfortunately, after all the effort and investment, Wi-Fi still did not work reliably, and lack of mobility/roaming was a huge headache for the forklifts. They even had lightning strike one of the poles the cables were hanging on, which fried a substantial portion of the setup. Basically, lots of equipment and maintenance cost with no reliable connectivity.
Key considerations for moving to private wireless
Luca was convinced about the need to move to private wireless, but the biggest challenge was the availability of cellular devices for connecting to their AGVs (Automated Guided Vehicles) and to the tablets used in the forklifts, which natively support Wi-Fi, but not private 4G/5G. To solve this, they retrofitted the AGVs and forklifts with cellular gateways and modules. For AGVs, they connected cellular gateways directly to the PLC inside the AGV with NAT (Network Address Translation), and they disabled the Wi-Fi. This meant that the AGV vendor didn’t have to make any software or hardware changes. The gateway is small, fitting right inside the AGV, so nothing is seen from the outside once the latch is closed. The picture below shows how the gateway is connected to the PLC, and where the antennas are placed. That’s Luca on the right, and me on the left, admiring the finished product!
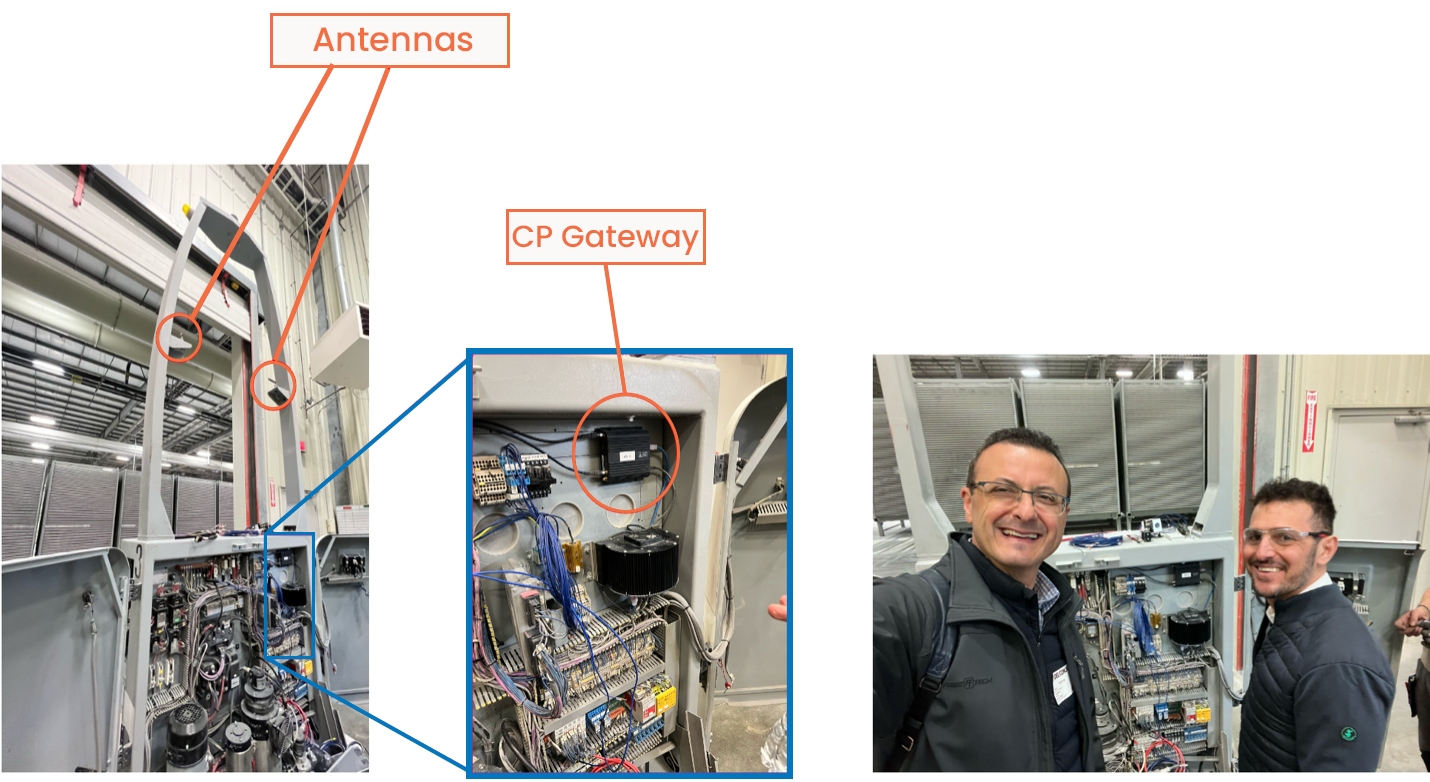
The bigger challenge was connecting the ruggedized tablets used inside the forklifts. To solve this problem, Del Conca opened the tablets, removed the Wi-Fi module, and inserted a SIM translator and a Sierra M2 module directly connecting to the mini PCIe. You can see the details of the Sierra module and SIM translator inside the tablet on the left picture below. Luca was kind enough to take the pieces apart and show me separately (bottom right).
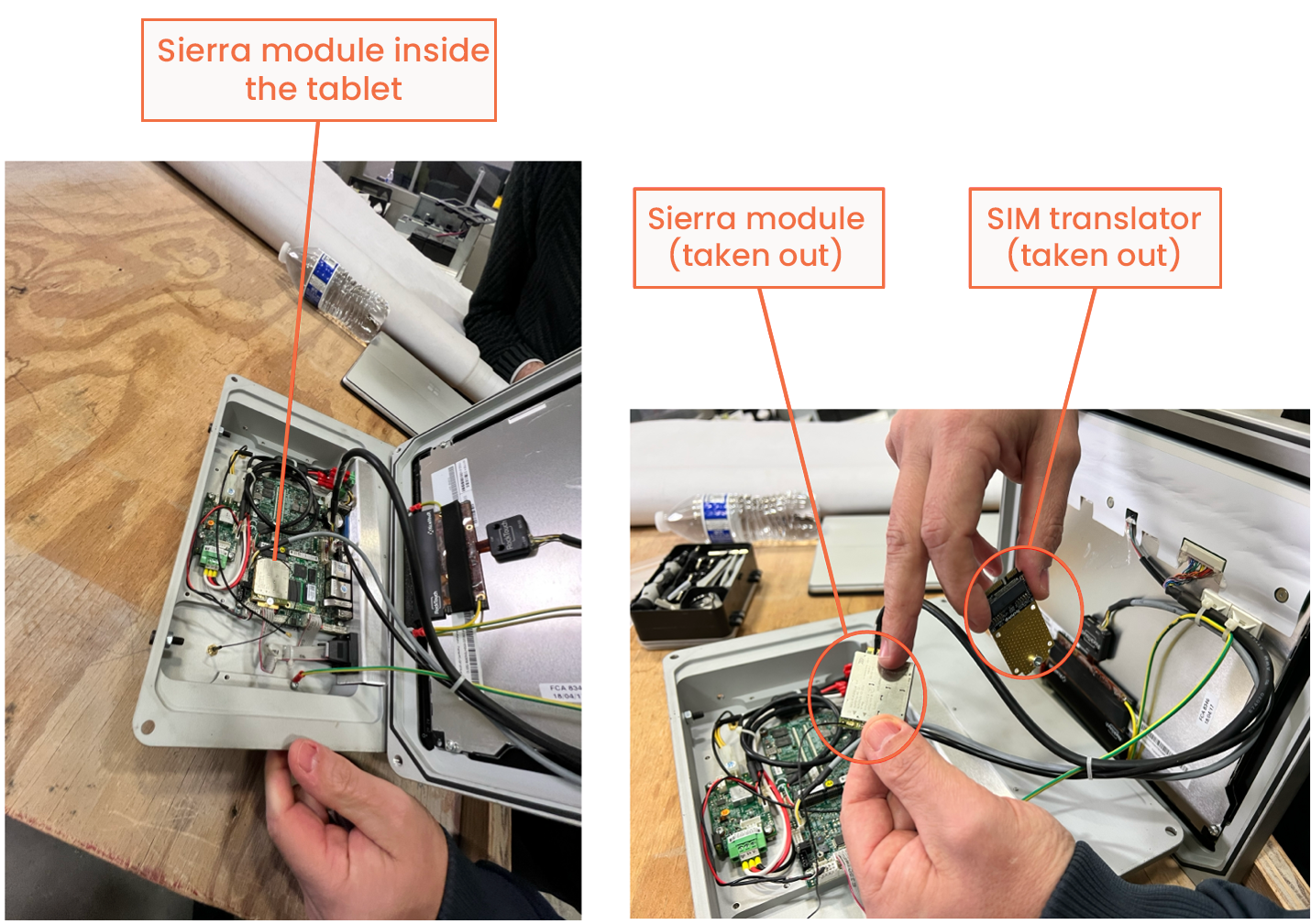
When the retrofit is completed, the upgraded tablet is re-installed in the forklift:
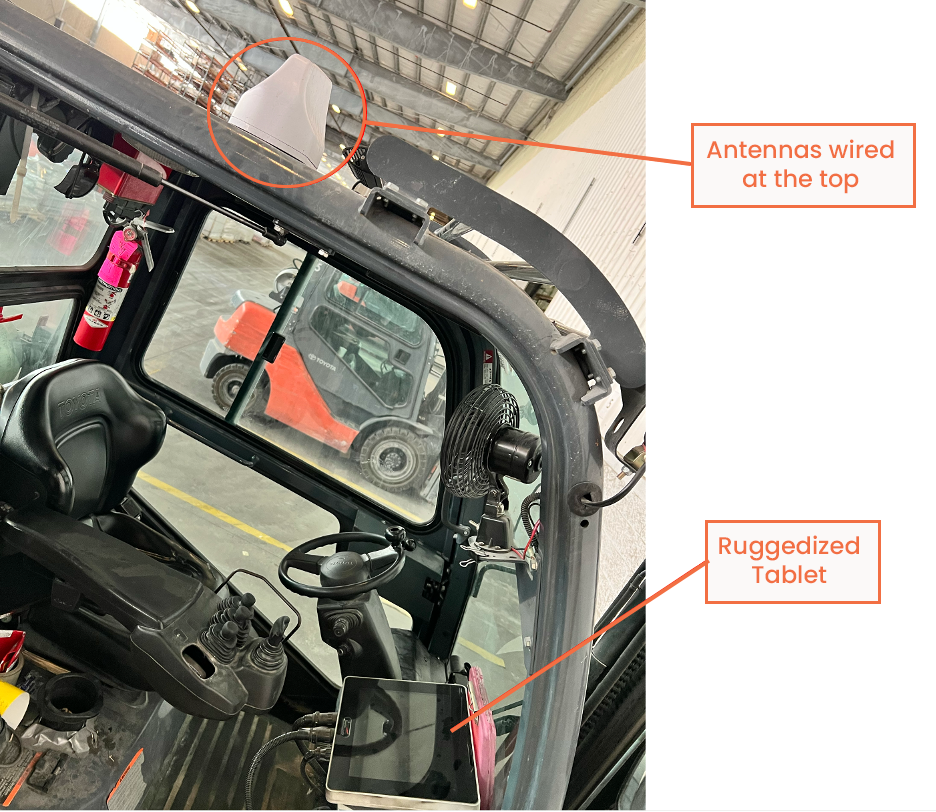
So was it all worth it? The ROI was significant.
The Celona Private wireless solution is 100% integrated into Del Conca, and any hiccup can really impact their operations. Freshly manufactured tiles keep coming from assembly line and AGVs constantly pick up tile stacks and move them. If the AGVs lose network connectivity and stop, then the whole plant operation would stop. If the tablets on the forklifts lose connection, forklift operators cannot get new work orders and trucks waiting outside cannot be loaded.
It did take some trial and error, but the resulting performance and reliability improvements justified all the hard work:
- AGVs are buzzing around constantly, operating autonomously and continuously on the private wireless network. The AGVs are key to operational efficiency, picking up stacks of tiles and moving them through final quality check and palletizing.
- Forklift operators get orders directly sent to their tablets with the specific location of pallets they need to pick up and drop off. Each forklift has an RFID tag, and their pick up and drop off locations are verified and recorded.
- With this new network, plant operations can be monitored remotely – even from Italy – since everything is connected to the corporate Intranet. If needed, anyone on the plant floor can connect to an expert using their tablet via a Teams session.
As a result of all these automation efforts, Luca said they significantly reduced the cost of operations and, more importantly, improved plant safety and reliability. As Luca mentioned in our recent webinar: “We went from about 2 days a month of service disruption with Wi-Fi to almost zero disruption with private wireless.”
Here is a quick video clip showing AGVs in action:
I want to thank Luca, Angelo, and the entire Del Conca team for allowing us to become a part of your artisan tile manufacturing operation!